SUMMARY
Simulation and digital twin technologies are essential tools in modern engineering and manufacturing, offering distinct yet complementary benefits. Simulation involves creating virtual models to predict system behavior during design and testing, focusing on specific scenarios with static, predefined conditions. In contrast, digital twins provide real-time, dynamic virtual representations of physical assets, continuously updated with live data for ongoing monitoring, predictive maintenance, and optimization. While simulations are crucial for early-stage testing, digital twins extend their utility across an asset’s lifecycle, enabling real-time insights and performance improvements. Together, they empower industries like automotive, aerospace, energy, and manufacturing to innovate and optimize effectively.
INDUSTRY
Automotive, Aerospace, Energy, Manufacturing
RESOURCES
In the world of modern engineering and manufacturing, simulation and digital twin technologies are often mentioned together. While both play a crucial role in optimizing processes and product development, they serve different purposes and offer unique capabilities. Understanding the distinction between these two concepts can help businesses choose the right tools for their specific needs.
In this blog post, we will explore the differences between simulation and digital twin, their applications, and how they contribute to the advancement of industries like automotive, aerospace, energy, and manufacturing.
What is Simulation?
Simulation refers to the process of creating a virtual model of a system, process, or product to predict its behavior under various conditions. Engineers use simulation software, like CAE (Computer-Aided Engineering) tools, to analyze aspects such as structural integrity, fluid flow, heat transfer, and mechanical performance. Simulations are typically conducted during the design and development phases, allowing engineers to test and refine concepts without the need for physical prototypes.

Key features of simulation include:
Virtual Testing: Simulations replicate the behavior of a system based on predefined models and parameters.
Hypothetical Scenarios: Engineers can run multiple simulations to predict how the product or system will behave under different conditions, such as stress, temperature, or load.
One-Time Analysis: Simulations are typically static, run once, or a few times, to evaluate specific scenarios.
What is a Digital Twin?
A digital twin goes beyond traditional simulation by creating a dynamic, real-time virtual representation of a physical asset, system, or process. It continuously updates using real-time data from sensors and other sources, allowing for ongoing monitoring, analysis, and optimization. A digital twin not only mirrors the current state of a physical object but also predicts future behavior based on both historical data and simulations.
Key features of a digital twin include:
Real-Time Data Integration: Digital twins are constantly fed with live data from physical assets, making them a dynamic and up-to-date representation.
Continuous Monitoring: Unlike simulations that are run at specific times, digital twins operate continuously, providing ongoing insight into the performance and health of a system.
Predictive and Prescriptive Analytics: Digital twins use real-time data to predict potential issues and suggest optimal solutions, helping with maintenance, performance optimization, and process control.

Core Differences Between Simulation and Digital Twin
Static vs. Dynamic Nature
Simulation: A simulation is generally static. It is run to evaluate a design or system based on fixed parameters and assumptions at a given time.
Digital Twin: A digital twin is dynamic. It evolves in real-time, continuously updating as it receives new data from the physical counterpart.
Timeframe and Purpose
Simulation: Primarily used for design and testing, simulations help predict performance during the design phase, often before physical prototypes are made.
Digital Twin: Digital twins are used across the entire lifecycle of an asset—from design and production to real-time monitoring and maintenance.
Data Input
Simulation: Simulations rely on predefined conditions, material properties, and models without real-time input from the actual system.
Digital Twin: Digital twins are fed with real-world data from sensors and devices attached to the physical object or process, making them more reflective of actual conditions.
Usage Scenario
Simulation: Useful for testing theoretical designs, making product decisions, and troubleshooting during early development.
Digital Twin: Ideal for real-time monitoring, predictive maintenance, operational optimization, and long-term system management.
Scope of Application
Simulation: Focuses on specific scenarios or testing under particular conditions to answer "what-if" questions.
Digital Twin: Encompasses the full lifecycle of a system or product, addressing both "what is happening now" and "what will happen" questions.
How Simulation and Digital Twin Work Together
Although simulation and digital twins differ in functionality, they can complement each other in powerful ways. A digital twin often incorporates simulation as part of its modeling, using predictive simulations to forecast the future behavior of a system based on real-time data.
For example:
A simulation might predict how a component will behave under stress during the design phase.
A digital twin of that same component, once deployed in the field, would continuously monitor its stress levels using sensor data. If abnormal conditions arise, the digital twin can use simulation to predict the likelihood of failure and suggest preventive measures.
In this way, simulations help develop the initial models used in digital twins, while digital twins extend the use of these models throughout the asset’s lifecycle.
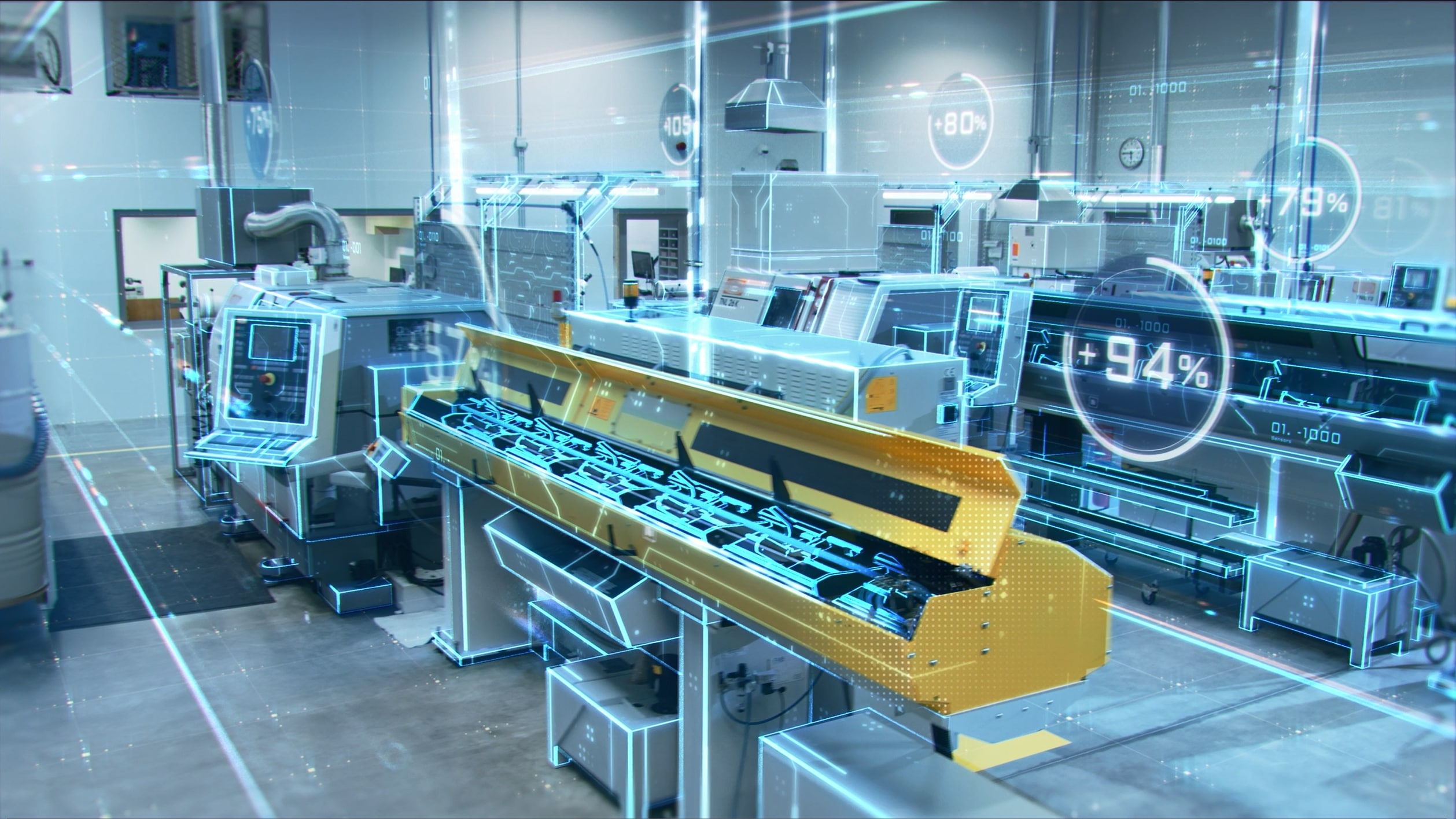
Applications of Simulation and Digital Twins
Automotive Industry
Simulation: Used to test vehicle designs, optimize aerodynamics, and evaluate safety features like crashworthiness.
Digital Twin: Deployed for real-time monitoring of connected vehicles, optimizing performance, and predicting maintenance needs based on actual driving data.
Aerospace
Simulation: Helps engineers evaluate flight dynamics, structural integrity, and propulsion systems during aircraft development.
Digital Twin: Continuously monitors the condition of aircraft in service, improving maintenance schedules and ensuring safety by predicting component wear.
Energy
Simulation: Used to model fluid flow in turbines, heat transfer in boilers, and energy efficiency in power plants.
Digital Twin: Provides real-time monitoring of power generation assets, optimizing energy output, and detecting potential issues before they impact operations.
Manufacturing
Simulation: Helps test the feasibility of production processes like casting, molding, or additive manufacturing.
Digital Twin: Tracks machinery health, production efficiency, and quality control, allowing for real-time adjustments to improve performance.
Conclusion: Choosing the Right Approach
Both simulation and digital twins play critical roles in modern engineering and manufacturing. While simulation provides powerful tools for design, testing, and validation, digital twins offer an ongoing, real-time view of assets and processes throughout their lifecycle. Together, they can significantly enhance operational efficiency, reduce downtime, and improve product quality.